Yokogawa Electric, a Tokyo-headquartered electrical engineering and software company, is celebrating its 110th anniversary this year (just like The Northern Miner!) with a new strategy to manage mining operations from start to finish.
The multinational, which has extensive experience working with tier-one mining companies, has introduced End-to-End (E2E) optimization to enhance efficiency, address evolving ore processing needs, and meet ESG and cost demands.
“Over the years, mining companies have implemented automation, predictive maintenance and energy efficiency initiatives that have improved some aspects of their operations,” Vice-President Naohisa Endo says. “But they remain fragmented solutions optimizing individual processes rather than the entire operation.
“By leveraging our expertise in process control, AI-driven analytics and digital transformation, we help mining companies transition from isolated optimizations to a connected, system-wide approach,” said Endo, who heads the company’s Materials business.
According to Endo, the requirement for improved control and oversight of the entire process – encompassing extraction, crushing, grinding, flotation, concentration/dewatering and tailings disposal – is critical for mining companies coping with evolving challenges.
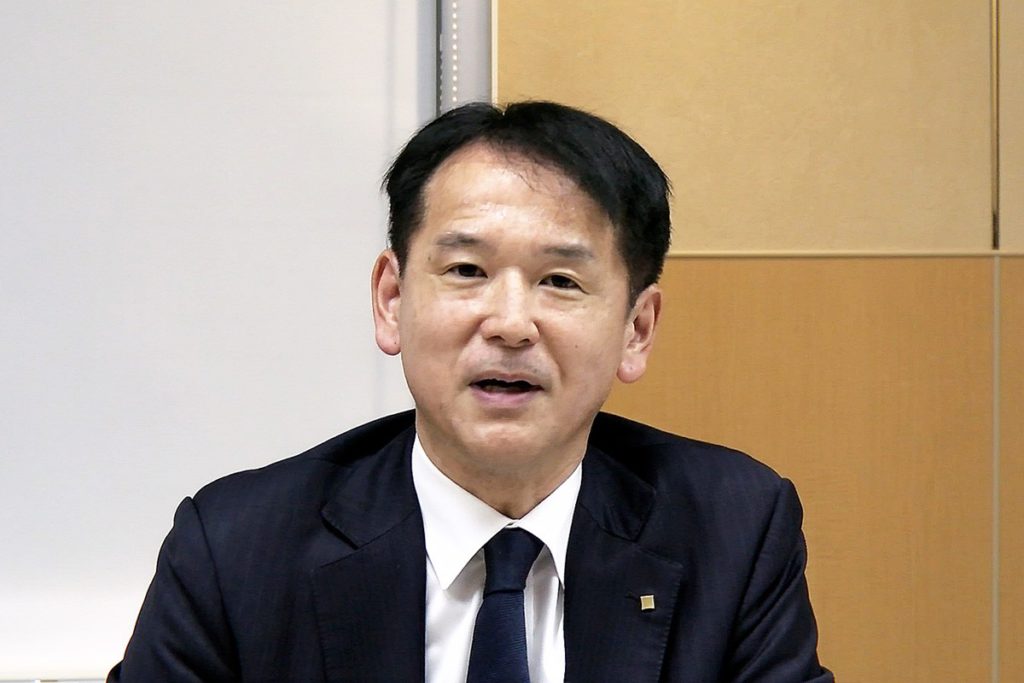
Endo highlights that as ore bodies become more complex and operational demands increase, mining companies are seeking new ways to get the most out of their resources while maintaining efficiency. He cites the International Institute for Sustainable Development’s report that mining emits between 1.9 and 5.1 gigatons of carbon dioxide annually as another challenge impacting mining company operations.
The application of E2E optimization can reduce costs through efficiencies in the crushing and grinding circuit by eliminating bottlenecks and using less energy, he says. Increased yields are also possible as a result of concentration recovery improvements and better management of reagent costs and tailings disposal, while predictive maintenance can reduce downtime.
“To unlock real efficiency and create long-term value, optimization must be approached holistically,” said Endo. “The industry needs to move from incremental improvements to an integrated operational strategy.”
E2E optimization connects the entire mining operation with each part working in harmony – not in isolation. Endo cites three critical components of E2E optimization:
- Real-time data integration that brings together data from crushing, grinding, concentration, energy usage and maintenance;
- AI-driven control that continually analyzes and adjusts operations as conditions change;
- Coordinated decision-making that aligns planning, maintenance and sustainability targets into one single framework.
A comprehensive E2E platform centralizes key performance indicator (KPI) information from each process by focusing on critical metrics like throughput, energy efficiency and recovery rates.
“By monitoring these process-level KPIs in an integrated manner, mining operations can gain unprecedented visibility into their entire value chain,” Endo said.
Implementing E2E optimization
Yokogawa breaks down silos and unifies data by integrating legacy systems with new technology platforms. The company builds interfaces that facilitate communication between different systems and components. This enables the monitoring of critical KPIs across all of the mining company’s inputs and outputs, its value chain.
Replacing the fixed settings on process controls with real-time monitoring and AI-driven adjustments, mining companies are better able to predict equipment failures. This is made possible by using predictive maintenance and advanced analytics that provide insights as they appear for informed decision-making across processes.
Aligning operational and strategic goals ensures that production, asset management and ESG objectives are in synch.
“Mining needs are constantly evolving in terms of technologies, data volumes and operational requirements,” Endo said. “We focus on building platforms with modular components that allow for easy addition, removal or swapping of specific functionalities as processes evolve or new technologies emerge.”
Mining companies embracing E2E optimization can gain a clear competitive edge by unlocking the full potential of available resources, reducing energy consumption while maintaining throughput, and improving recovery rates without increasing costs, he said. Companies can also meet sustainability goals while maintaining competitiveness, and enhance worker safety by reducing the need for manual interventions, he added.
Yokogawa has 17,000 employees across 60 countries and has extensive experience in the global mining industry. The company is engaged in discussions with several tier one mining companies about E2E optimization.
“These conversations indicate growing industry interest in more comprehensive solutions as traditional methods reach their practical limits,” Endo said. “Given the potential for increased productivity, improved safety and sustainability benefits, the business case is compelling.”
The preceding Joint Venture Article is PROMOTED CONTENT sponsored by Yokogawa Electric and produced in co-operation with The Northern Miner Group. Visit: https://www.yokogawa.com/industries/mining-metal/ for more information.
Be the first to comment on "JV Article: Why end-to-end optimization isn’t optional "