I was never really one for keeping a diary; I’m basically too lazy, and not nearly introspective enough. The only time I did keep one, it was by accident. In 1996 I was sent to Iran to supervise a drill program at a gold project called Zarshuran. It didn’t go well. A perfect storm of terrible rock conditions and inept local drillers doomed us before we’d even started. The drillers were the most comical I have ever hired; they lacked talent and common sense, and the managers couldn’t be trusted to sit the right way on a toilet. We drilled seven holes in three long months and they cost us a whole world of pain and frustration, yielding awful core recoveries and not enough data to make a decision on the project.
I faxed a daily drill report to London via a dodgy satellite phone at the camp. As summer dragged into autumn and winter set in, we were only getting 1-2 metres of core a day, the water pipes froze every night, and my daily reports got more and more fraught until drilling finally ground to a halt. Happily, my boss at the time (thanks Dave) realized a) that I was documenting a slow decline into lunacy, and b) kept the daily reports, bound into a single document; a diary of my misadventures which was presented to me at the office Christmas party that year. This piece is based on the daily faxes which I still have, 26 years later.
Zarshuran (“The place of the gold washing”), was 7,500 ft. up a mountain, six hours northwest of Tehran. It’s a Getchell-style Carlin gold system which had an active arsenic mine hosted in marbles (arsenic and gold often go hand in hand in similar gold systems in Nevada.) Rather than bring in a western drill company and battle Iranian customs for months, we decided to use an Iranian drill contractor that I’ll call COREO. They claimed that they could handle diamond core drilling, so we hired them after a due diligence visit to a drill site near Shiraz where they were drilling concrete grout holes in crumbly bedrock for a dam project.

General view of the Zarshuran gold project. Credit: Ralph Rushton
When two drillers finally did arrive, they had no accommodation, food, or toilets. They were kipping in a 12-metre container and using the hillside as their loo, which made soil sampling somewhat hazardous. One of my early reports noted dryly “morale is generally at a low ebb due to the poor living conditions and lack of head office backup.”
COREO eventually sent a project manager to site, Mr. Paknejad, who at first tried to manage the project remotely from his office 1,000 km away in Shiraz. In the one and only site meeting we had, akin to trying to have a calm chat with an hysterical five-year-old, he told me that “…mobilization would finish when he said it was finished and not before, and anyway who were we to question him (hint: the client) and besides, he was doing us a huge bloody favour sending anything to site.” He then jumped in his truck and buggered off to the nearest town to make a phone call to head office. He never returned, judging correctly that the bad-tempered foreigners who’d questioned his competence might not welcome him back on site.
A few days into the drill program and progress was painfully slow, as little as 2-3 metres per shift. We did what we could with the gear available, advised by Dave, an experienced Australian drilling consultant we’d retained to knock COREO’s crew into shape. Dave was a force of nature. Built like a haystack, his eyes looked in two different directions at the same time, and he couldn’t sit still for long because of his hemorrhoids. But with driller’s hands the size of tennis rackets and a quiet but vaguely threatening way of speaking, his beastly demeanour terrified our Iranian friends. There was still no sign of Mr. Paknejad, and our core shack with space for 150 core boxes was looking a tad optimistic.
By mid-September, we were on our third COREO supervisor. He showed up on site wearing shiny black shoes, nice pants and a pressed white shirt, bless. My daily fax noted “I’m not quite sure what his role is as he doesn’t seem to know much about drilling and is a gemologist by training.” I not-so-politely suggested he put on some coveralls and some boots, which he did. He then sat down on a stack of greasy PQ drill rods and casually asked me what all the pipes were for before telling me to “shut up and stop shouting because I was only the geologist and HE was the manager.”
He piped down when Dave told him he’d have a hard time managing anything with a PQ core barrel stuck up his backside. He left two days later, shoes still shiny.
We’d filled four or five core boxes with crumbly sulphide gouge but had nothing else to show for it other than an unhappy drill company who’d over-estimated the level of ineptitude we were willing to put up with. COREO had misinterpreted our contract. They thought we were paying them a flat daily rate, so the longer the mobilization process took the more money they made. But we weren’t. We were paying by the metre with hefty penalties for poor recovery; unlike most of their clients, I’d actually read the contract. At 4 metres a shift, with only one machine running, their revenue was less than US$400 a day. We also knew they weren’t paying their drillers and they couldn’t source the PQ gear which they were obliged to provide.
Sept. 13 was the low point. Two operational machines, 3 metres of advance and only 70 cm of core. Ground conditions were still horrible. The mineralized zone was essentially black sulphide-rich clay with random blocks of hard yellow orpiment up to 3-4 metres across. The host marble was the texture of wet sugar granules, not conducive to recovering much core.
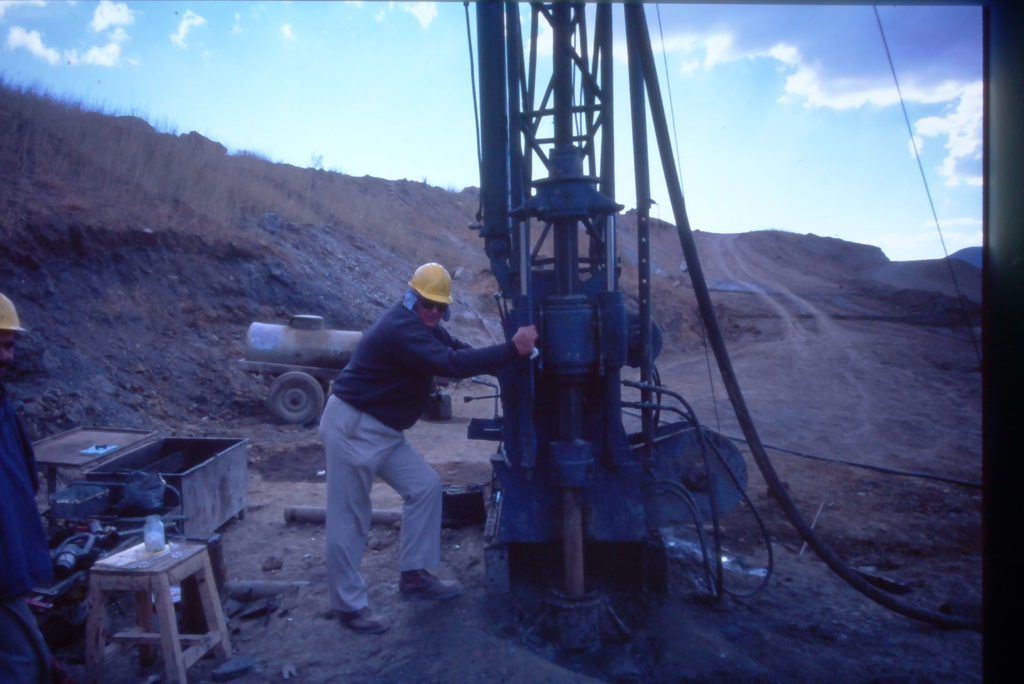
Australian drill consultant, Dave, takes charge of the drilling at Zarshuran. Credit: Ralph Rushton
COREO’s screw ups were endless. I found chunks of drill bit in the core boxes. The wireline cable snapped nearly taking a driller’s thumb off. The night shift’s diesel oil drum heater fell over, nearly incinerating a rig and its crew. An offsider dropped a PQ rod on his ankle breaking it. The fluid sumps were too small. A rod snapped at the top of the hole. They ran out of bentonite, super mix and plastic water pipe.
Eventually I snapped, leading to a shouting match with the new drill supervisor, Mr. Charifyan. Using some undiplomatic Anglo-Saxon cursing — which, thankfully, he couldn’t understand — I told him he should start bloody managing something and stop sleeping in his truck. In the heat of the moment I told him his IQ level was on a par with a domestic appliance I’d once owned, which was being generous. He left soon after once it dawned on him that we paid the bills and he worked for us, not the other way round. My final comment about him read “He is childish in the extreme and has no comprehension of the spirit of contracts or agreements. I now feel that I’ve been far too generous with COREO.”
In late October, winter arrived. We’d wake up to frozen water lines and hypothermic night shift drillers, and drilling would have to wait until the sun was up. Progress slowed to glacial: 2 metres of core from two holes in 36 hours. On Nov. 3 we got no progress from either machine and the writing was finally on the wall. I decided to shut the program down a few days later after COREO told me they wanted to re-drill a hole. The idea of spending another three weeks watching COREO’s clowns try to re-drill a hole in crappy ground in the middle of the winter was a non-starter.
Nov. 8 was demob day. COREO left with unnatural haste, far quicker than they’d arrived. Three flat beds and a crane showed up, the rigs were loaded and off they went down the mine road, getting away from me as fast as they could. We drilled from Sept. 1 to Nov. 8, completing 1,015 metres of core drilling, 15 metres per day between two machines. Those of you who’ve run drill programs will know how monumentally awful that is. A decent North American company would complete that in under a month even with bad rock conditions. And it wasn’t just the poor daily rate that hurt, it was the pain we went through with COREO’s management, day in day out. They’d convinced themselves they were actually a good drilling company. The constant fighting with them over everything from drill bits to shifty invoices had worn me out and I was badly in need of a break.
In terms of assays, the season was a roaring success. Our first hole cut 50 metres at about 11 grams gold per tonne from surface, passing right through the guts of a mineralized fault zone, hinting at a substantial gold system. So, the next year we were back at it with a larger drill program, and this time we were smarter — or so we thought — sacking COREO and hiring an Australian drill contractor that had a modern, truck-mounted, multipurpose drill rig parked up at BHP’s massive Reko Diq copper project in Pakistan. It seemed like a great idea at the time, that is before nuclear tests, corrupt customs officers and endless police check points conspired to screw up our best laid plans. But that’s for Part 2.
—Ralph Rushton is a geologist and has worked at mines and exploration projects around the world including stints in South Africa, Turkey, Bulgaria, Yemen, Iran and Pakistan. He is currently the president of Aftermath Silver, a silver development company with projects in Chile and Peru. In his spare time, he writes about mining and exploration for his popular blog, urbancrows.com.
Ralph, your experience is pretty much the same as mine in 1996-1997 while supervising an exploration project in Kyrgyzstan. Unfortunately for us however the assay results after nearly two frustrating years were not encouraging. It was an experience which tested me mentally and physically.