A report commissioned by Glasgow-based engineering company the Weir Group warns that the total amount of power used in hard rock mining is equal to 12 exajoules per year or close to 3.5% of global energy use and that the industry must move away from legacy systems and processes if it wants to meet sustainability targets.
After analyzing mine energy data from over 40 studies published from 2007 to 2020 and which focused on five commodities – copper, gold, iron ore, nickel and lithium – comminution was identified as the single biggest user of energy at mine sites, typically accounting for 25% of the mining industry’s final energy consumption.
“Extended across all hard rock mining, this is equivalent to the power used by 221 million typical U.K. homes, or c.1% of total consumption globally,” the report says. “Comminution is, therefore, a natural target for the most impactful energy savings opportunities.”
Gold mining
In the gold mining sector, most studies reviewed for the report estimated that the overall average energy consumption is approximately 134 GJ/kg of gold for underground mines and average energy consumption of 372 GJ/kg of gold for open-pit operations.
The split between what is consumed for mining operations and what’s attributed to processing plants is almost equal in most cases, with the latter usually being one or two percentage points higher, according to the report.
Copper mining
Comparing what the literature shows with a database of 400 mine sites, it is possible to conclude that copper production has an average energy intensity of approximately 25 GJ/t of copper, the report says.
Averaging all of those mines, the report’s found that about 55% of total site energy is in the mining operations with the remainder of energy consumption occurring in the processing plant.
“Energy use in the mining operations is 40% electricity (primarily ventilation) and 60% diesel (for loading and hauling). In the processing plant, the majority of energy consumption occurs in grinding (90%) with the remaining energy consumption in this study being attributed to flotation,” the document reads.
Nickel mining
The energy intensity of nickel laterite processing — high-pressure acid leach, enhanced pressure acid leach and heap leach — is relatively high at an average of 244 GJ/t of nickel.
“With laterite processing expected to increase in coming years, to meet increased nickel demand, the overall energy consumption in this industry is expected to increase,” the report states.
Nickel sulphide processing, on the other hand, averages an energy intensity for concentrators of 31 GJ/t of nickel produced. Of this, the split between mining and processing is approximately 50:50 — with then 90% of the processing plant energy consumption being used in comminution.
“Given the overall nickel sulphide energy intensity of ~200 GJ/t of nickel, the concentrators are only a relatively small portion of overall energy footprint,” the paper notes.
Lithium mining
Under the premise that hard rock lithium mining is likely to dominate in coming years due to the trend towards low/no cobalt batteries, which tend to use lithium hydroxide rather than lithium carbonate, the study indicates that energy requirements for a lithium concentrator are approximately 15 GJ/t lithium produced. Of this, 60% of energy consumption is electricity in the concentrator with the remaining 40% in the mining operations.
In the processing plant, the largest portion of energy consumption was identified to be in the crushing area, followed by dense media separation. Crushing accounts for about 20% of site energy consumption, with a further 7% in the regrind mill.
Iron ore
In hematite operations, the report found that energy intensity averages less than 0.15 GJ/t of iron ore, taking into account both diesel consumption in the mine and electricity production in the processing plants.
Approximately 90% of the energy consumption was determined to be diesel consumption in mobile equipment, while the remaining energy consumption is electricity in processing plants — mostly crushing and conveyors.
In magnetite operations, the paper showed that energy intensity for processing is 0.23 GJ/t of shipped ore, including the additional separation and concentration equipment. Mining operations add up to an additional 0.16 GJ/t of shipped ore giving a total site energy intensity of 0.3 GJ/t of shipped ore.
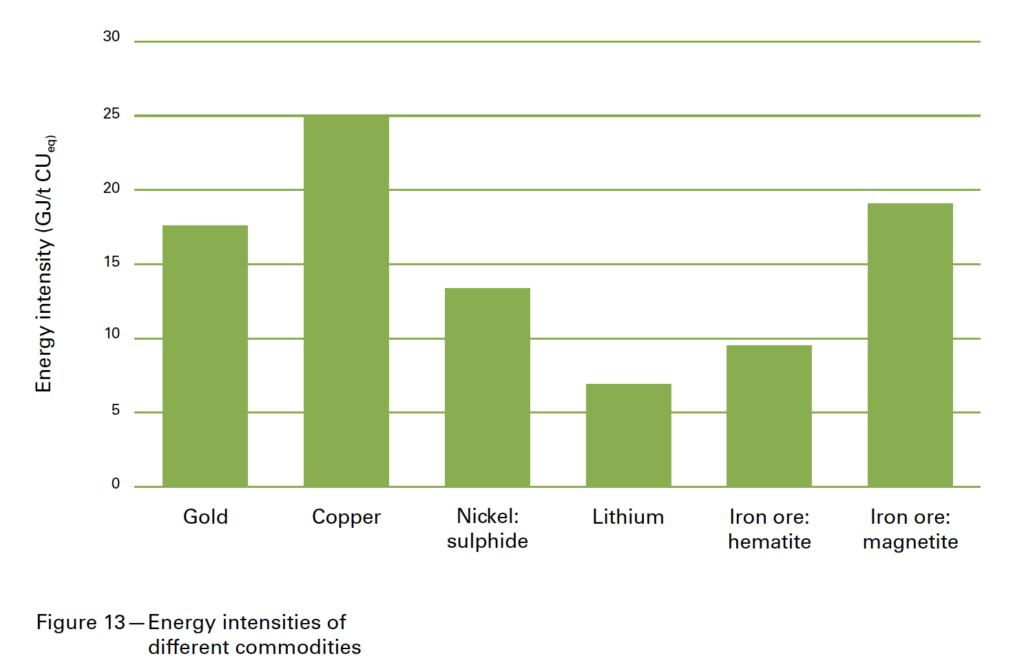
How to cut energy consumption
According to the document, small improvements in comminution technologies can lead to relatively large savings in both energy consumption and greenhouse gas emissions. As an example, the report presents the idea of a 5% incremental improvement in energy efficiency across comminution, which could result in greenhouse gas emissions reductions of more than 30 million tonnes of CO2e.
“The replacement of traditional comminution equipment with new grinding technology also reduces indirect emissions in the mining value chain, for example by removing the need for the manufacture of emission-intensive steel grinding balls. Of the remaining energy consumption by the mining industry, diesel in varied forms of mobile equipment accounts for 46%, electricity in mining (ventilation) 15% and ‘other electricity’ 14%,” the report states.
Reducing energy consumption could also be achieved by optimizing grinding circuits, particularly when designing them for greenfield or when expanding brownfield sites.
“Advancements in high pressure grinding rolls, high intensity grinding and stirred mills/vertical mills mean that traditional semi-autogenous grinding/ball mill applications could be replaced and the same outcomes achieved —subject, of course, to the amenability of the particular ore type and processing requirements to these comminution circuits,” according to the report.
The paper notes that additional throughput in grinding circuits as a result of energy savings unlocking additional energy capacity should form part of business cases when exploring the potential of equipment and circuit changes.
Similarly, the report found that a good case could be built around automating operations so that computing technology and big data are able to provide high-fidelity block models showing mineral concentration and composition throughout mining areas.
Big data and artificial intelligence are also mentioned as key to optimizing processing and reducing energy consumption.
Becoming a zero-emissions industry is also presented as a possibility if zero-emission energy sources are deployed for mining equipment. Renewable energy, energy storage and alternative fuels are mentioned as viable options which, in turn, would leave a relatively small role for offsets and carbon credits to play.
“The report comes as the mining industry is under ever-greater pressure to produce essential minerals that support some of the biggest global structural trends,” the study says. “Copper, nickel, steel and lithium are core components of electricity transmission and storage, electric vehicles and renewable energy infrastructure. The move to a decarbonized economy will result in increased primary consumption of these mined commodities, even after factoring for recycling, so it is important that mining itself becomes more sustainable.”
Be the first to comment on "Mining legacy processes setting the industry behind in sustainability targets – report"